What is Porosity in Welding: Understanding Its Reasons and Enhancing Your Abilities
What is Porosity in Welding: Understanding Its Reasons and Enhancing Your Abilities
Blog Article
Porosity in Welding: Identifying Common Issues and Implementing Finest Practices for Prevention
Porosity in welding is a pervasive issue that frequently goes unnoticed till it triggers significant troubles with the stability of welds. In this discussion, we will certainly discover the vital factors adding to porosity formation, analyze its destructive effects on weld efficiency, and discuss the ideal practices that can be embraced to lessen porosity occurrence in welding processes.
Common Root Causes Of Porosity
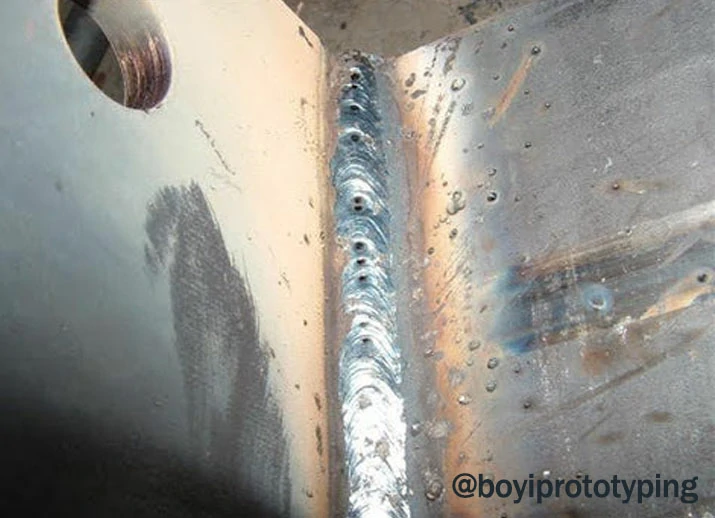
Using unclean or wet filler materials can introduce pollutants right into the weld, adding to porosity concerns. To reduce these usual reasons of porosity, comprehensive cleansing of base metals, proper protecting gas selection, and adherence to optimum welding parameters are important methods in attaining premium, porosity-free welds.
Impact of Porosity on Weld Quality

The presence of porosity in welding can substantially jeopardize the structural honesty and mechanical homes of welded joints. Porosity produces gaps within the weld steel, weakening its total strength and load-bearing capability.
Among the main repercussions of porosity is a reduction in the weld's ductility and toughness. Welds with high porosity levels tend to exhibit reduced impact toughness and reduced ability to flaw plastically before fracturing. This can be especially worrying in applications where the bonded parts undergo vibrant or cyclic loading conditions. In addition, porosity can restrain the weld's capability to effectively transmit pressures, bring about premature weld failing and prospective safety threats in vital structures.
Best Practices for Porosity Prevention
To enhance the structural stability and top quality of bonded joints, what certain steps can be implemented to reduce the event of porosity throughout the welding procedure? Porosity prevention in welding is essential to make sure the integrity and strength of the last weld. One effective method is appropriate cleansing of the base metal, removing any kind of contaminants such as corrosion, oil, paint, or dampness that can lead to gas entrapment. Making certain that check this site out the welding equipment is in good problem, with clean consumables and ideal gas flow rates, can likewise significantly official statement minimize porosity. Additionally, maintaining a stable arc and regulating the welding specifications, such as voltage, present, and take a trip speed, aids produce a constant weld pool that minimizes the danger of gas entrapment. Using the proper welding method for the details product being welded, such as readjusting the welding angle and weapon position, can additionally protect against porosity. Routine inspection of welds and prompt remediation of any concerns determined during the welding process are necessary practices to prevent porosity and generate high-quality welds.
Significance of Appropriate Welding Strategies
Implementing appropriate welding techniques is critical in making sure the structural stability and high quality of bonded joints, building on the structure of effective porosity avoidance steps. Welding techniques directly affect the total strength and longevity of the welded framework. One essential element of correct welding strategies is preserving the correct warmth input. Excessive heat can result in raised porosity as click here for more a result of the entrapment of gases in the weld swimming pool. Alternatively, inadequate warm might lead to insufficient combination, creating prospective weak factors in the joint. Furthermore, making use of the suitable welding parameters, such as voltage, current, and travel speed, is crucial for accomplishing audio welds with very little porosity.
In addition, the choice of welding procedure, whether it be MIG, TIG, or stick welding, must align with the particular needs of the job to make sure optimal results. Correct cleaning and preparation of the base metal, as well as choosing the right filler material, are additionally crucial parts of competent welding strategies. By sticking to these ideal techniques, welders can minimize the risk of porosity development and produce premium, structurally sound welds.
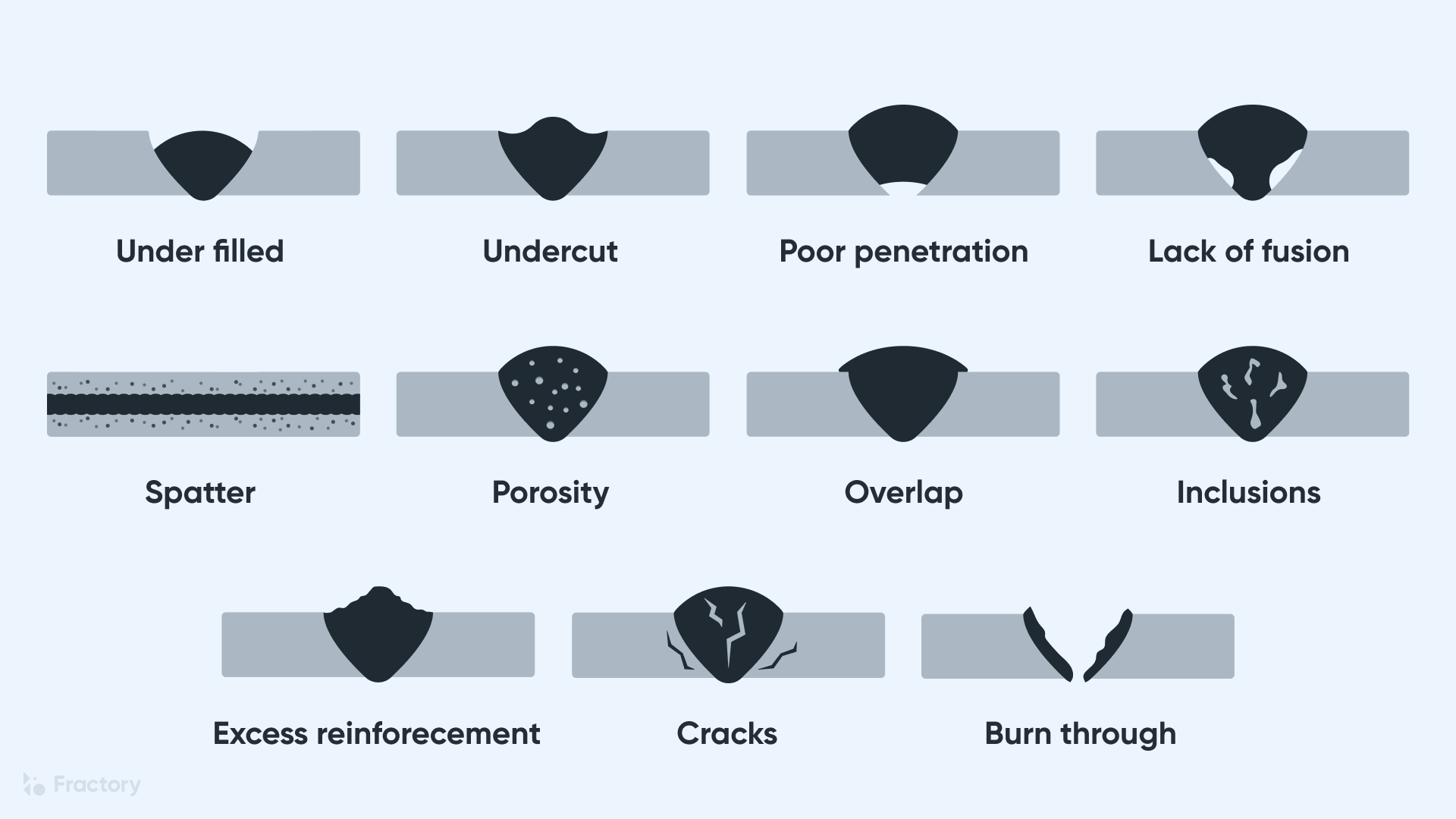
Checking and Quality Assurance Actions
Testing treatments are necessary to find and protect against porosity in welding, making sure the stamina and toughness of the final item. Non-destructive testing methods such as ultrasonic testing, radiographic testing, and aesthetic inspection are typically used to identify possible flaws like porosity.
Performing pre-weld and post-weld examinations is likewise critical in maintaining high quality control criteria. Pre-weld examinations involve confirming the materials, tools setups, and sanitation of the work location to avoid contamination. Post-weld assessments, on the various other hand, evaluate the last weld for any issues, consisting of porosity, and confirm that it satisfies specified requirements. Carrying out an extensive quality assurance plan that consists of complete testing procedures and assessments is critical to minimizing porosity issues and guaranteeing the overall high quality of bonded joints.
Conclusion
In conclusion, porosity in welding can be a typical concern that impacts the high quality of welds. By recognizing the common sources of porosity and applying finest practices for avoidance, such as correct welding strategies and screening procedures, welders can make sure high quality and dependable welds. It is important to focus on avoidance methods to reduce the occurrence of porosity and keep the integrity of bonded structures.
Report this page